Continuous Improvement: A Positive Feedback Loop Towards Operational Excellence
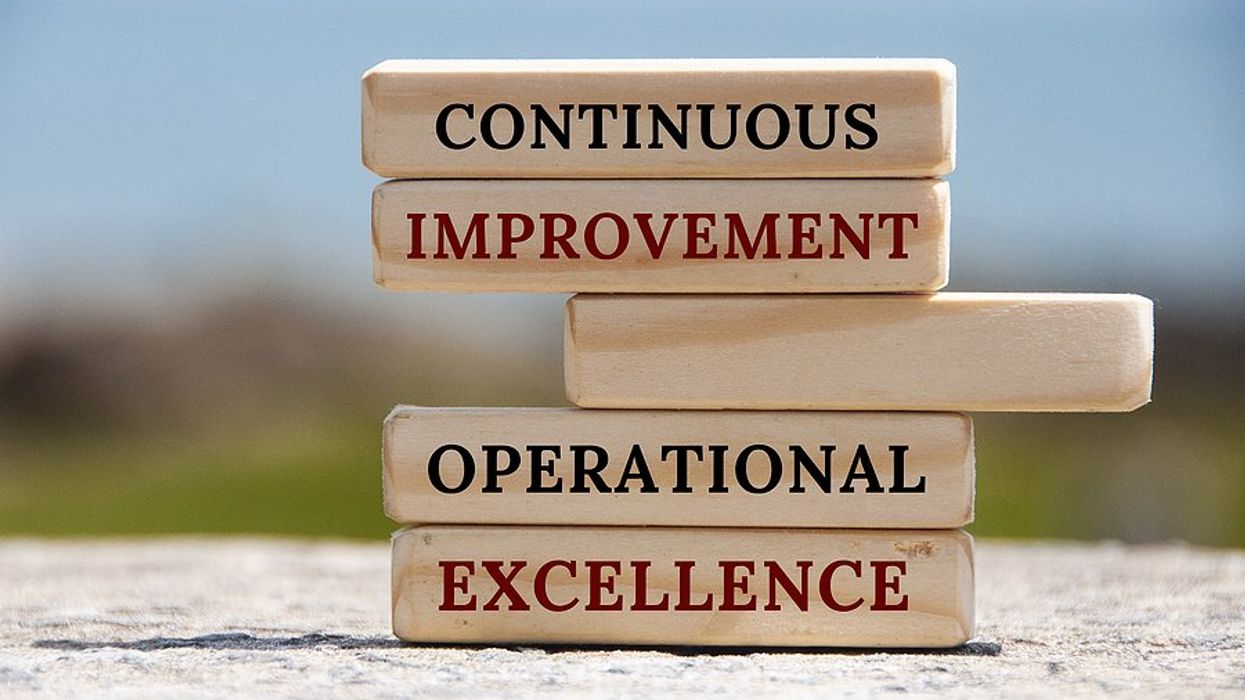
Are your organization’s operations more status quo—don’t fix what’s not broken? It may not be broken, but business changes, emerging technologies, and evolving regulatory requirements are inevitable. If your organization isn’t changing, then it may become stale and irrelevant. Continuous improvement helps the organization adapt in response to changes and also drives efficiency and innovation.
If your organization hasn’t implemented a continuous improvement process, how can you get started? The first step is to build a culture that encourages and supports continuous improvement. Develop a culture that fosters a curious mindset enabling employees to identify and address inefficiencies in processes and systems, which leads to improved efficiencies and better outcomes.
Benefits Of Continuous Improvement
Bigstock
When you’re continuously improving, this promotes innovation within the organization. Encourage employees to challenge the status quo and seek better ways to do things. This will enable employees to identify and evaluate inefficiencies and to come up with innovative solutions to problems and challenges, which will improve processes, products, and services. This, in turn, can help the organization optimize operations, achieve higher levels of performance, and even potentially mitigate risks to prevent incidents or failures.
Another benefit of continuous improvement is that it encourages employee engagement. Engaged employees are more likely to be productive, motivated, and committed to the organization's success. Empower employees to take ownership and drive improvements by contributing their ideas, insights, and suggestions for improvement. Don’t forget to acknowledge and celebrate the employees’ continuous improvement contributions. This will inspire others, build momentum, and create a positive feedback loop that encourages more continuous improvement initiatives.
Provide employees with the appropriate tools (including skills, knowledge, and resources) for their continuous improvement efforts. Support employees with the training and ongoing professional development they need. There are various training and certifications available to effectively implement different continuous improvement methodologies, tools, and techniques. You may also need to provide access to resources such as relevant data.
Continuous Improvement Methodologies, Tools, And Techniques
Bigstock
There are several methodologies, tools, and techniques to implement continuous improvement. If you’re just starting, one of the simpler approaches is PDCA (Plan-Do-Check-Act), which is known as the Deming Cycle. It’s a continuous improvement model that involves planning, implementing, checking, and acting on changes in a systematic way. It’s a cyclical process of identifying opportunities for improvement and then planning, implementing changes, checking the results, and acting on lessons learned. For example, your business partner wants to implement an unused module within enterprise resource planning (ERP). In addition to the technology, take the opportunity to look broader and see which business processes up/downstream could benefit from being updated at that same time.
Other more formal methodologies are Agile, Lean, and Six Sigma. Six Sigma, for example, is very formal (define, measure, analyze, improve, and control) and has a certification wherein belt colors indicate the level of training, knowledge, and expertise. Each approach is different and depending on your organization’s needs and goals; one or more may align better than others. Also, the approaches aren’t mutually exclusive so you can adopt more than one of them.
When your organization is continuously improving (and not just maintaining the status quo), it’s able to respond to changes and challenges, be more resilient and competitive, and, ultimately, promote operational excellence. So, foster a culture that encourages and supports continuous improvement initiatives.
For more information on the benefits of continuous improvement, follow me on LinkedIn!
- Lean Principles Of Waste In Engineering ›
- Process Control: Do You Have Dandelions In Your Yard? ›
- 4 Ways Organizations Can Implement Root Cause Analysis Procedures (And How It Benefits Them) ›
- 5 Operational Challenges That Could Derail Your Business - Work It Daily ›
- How To Drive Innovation In The Workplace - Work It Daily ›